Make: Electronics by Charles Platt (read me a book .TXT) ๐
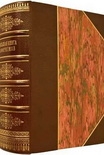
Read free book ยซMake: Electronics by Charles Platt (read me a book .TXT) ๐ยป - read online or download for free at americanlibrarybooks.com
- Author: Charles Platt
Read book online ยซMake: Electronics by Charles Platt (read me a book .TXT) ๐ยป. Author - Charles Platt
This time Iโd like you to align the wires parallel with each other. Joining them this way is a little more difficult than joining them when they cross each other, but itโs a necessary skill. Otherwise, you wonโt be able to slide heat-shrink tubing over the finished joint to insulate it.
Figures 3-40 through 3-44 show a successful joint of this type. The two wires do not have to make perfect contact with each other; the solder will fill any small gaps. But the wires must be hot enough for the solder to flow, and this can take an extra few seconds when you use the low-wattage pencil-style iron.
Be sure to feed the solder in as shown in the pictures. Remember: donโt try to carry the solder to the joint on the tip of the iron. Heat the wires first, and then touch the solder to the wires and the tip of the iron, while keeping it in contact with the wires. Wait until the solder liquifies, and you will see it running eagerly into the joint. If this doesnโt happen, be more patient and apply the heat for a little longer.
Figure 3-40.
Figure 3-41.
Figure 3-42.
Figure 3-43. This and the preceding three figures show how joining two wires that are parallel is more difficult, and the low-wattage, pencil-type soldering iron will require longer to heat them sufficiently for a good joint. Thinner solder can be used.
Figure 3-44. The finished joint has enough solder for strength, but not so much solder that it will prevent heat-shrink tubing from sliding over it.
Tools
Desoldering
Desoldering is much, much harder than soldering. Two simple tools are available:
Suction pump. First, you apply the soldering iron to make the solder liquid. Then you use this simple gadget to try to suck up as much of the liquid as possible. Usually it wonโt remove enough metal to allow you to pull the joint apart, and you will have to try the next tool. Refer back to Figure 3-10.
Desoldering wick or braid. Desoldering wick, also known as braid, is designed to soak up the solder from a joint, but again, it wonโt clean the joint entirely, and you will be in the awkward position of trying to use both hands to pull components apart while simultaneously applying heat to stop the solder from solidifying. Refer back to Figure 3-11.
I donโt have much advice about desoldering. Itโs a frustrating experience (at least, I think so) and can damage components irrevocably.
Theory
Soldering theory
The better you understand the process of soldering, the easier it should be for you to make good solder joints.
The tip of the soldering iron is hot, and you want to transfer that heat into the joint that you are trying to make. In this situation, you can think of the heat as being like a fluid. The larger the connection is between the soldering iron and the joint, the greater the quantity of heat, per second, that can flow through it.
For this reason, you should adjust the angle of the soldering iron so that it makes the widest possible contact. If it touches the wires only at a tiny point, youโll limit the amount of heat flow. Figures 3-45 and 3-46 illustrate this concept. Once the solder starts to melt, it broadens the area of contact, which helps to transfer more heat, so the process accelerates naturally. Initiating it is the tricky part.
The other aspect of heat flow that you should consider is that it can suck heat away from the places where you want it, and deliver it to places where you donโt want it. If youโre trying to solder a very heavy piece of copper wire, the joint may never get hot enough to melt the solder, because the heavy wire conducts heat away from the joint. You may find that even a 40-watt iron isnโt powerful enough to overcome this problem, and if you are doing heavy work, you may need a more powerful iron.
As a general rule, if you canโt complete a solder joint in 10 seconds, you arenโt applying enough heat.
Figure 3-45. With only a small surface area of contact between the iron and the working surface, an insufficient amount of heat is transferred.
Figure 3-46. A larger area of contact between the soldering iron and its target will greatly increase the heat transfer.
Adding Insulation
After youโve succeeded in making a good inline solder connection between two wires, itโs time for the easy part. Choose some heat-shrink tubing that is just big enough to slide over the joint with a little bit of room to spare.
Figure 3-47. Other members of your family should understand that although a heat gun looks like a hair dryer, appearances may be deceptive.
Heat Guns Get Hot, Too!
Notice the chromed steel tube at the business end of your heat gun. Steel costs more than plastic, so the manufacturer must have put it there for a good reasonโand the reason is that the air flowing through it becomes so hot that it would melt a plastic tube.
The metal tube stays hot enough to burn you for several minutes after youโve used it. And, as in the case of soldering irons, other people (and pets) are vulnerable, because they wonโt necessarily know that the heat gun is hot. Most of all, make sure that no one in your home ever makes the mistake of using a heat gun as a hair dryer (Figure 3-47).
This tool is just a little more hazardous than it appears.
Slide the tubing along until the joint is centered under it, hold it in front of your heat gun, and switch on the gun (keeping your fingers away from the blast of superheated air). Turn the wire so that you heat both sides. The tubing should shrink
Comments (0)