Make: Electronics by Charles Platt (read me a book .TXT) ๐
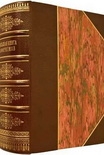
Read free book ยซMake: Electronics by Charles Platt (read me a book .TXT) ๐ยป - read online or download for free at americanlibrarybooks.com
- Author: Charles Platt
Read book online ยซMake: Electronics by Charles Platt (read me a book .TXT) ๐ยป. Author - Charles Platt
3. Trim the wires approximately with your wire cutters.
4. Make the joints with your pencil soldering iron. Note that in this circuit, you are just joining wires to each other. The components are so close together that theyโll prevent each other from wiggling around too much. If you are using board with copper pads (as I did), and some solder connects with them, thatโs OKโas long as it doesnโt creep across to the neighboring component and create a short circuit.
5. Check each joint using a close-up magnifying glass, and wiggle it with pointed-nosed pliers. If there isnโt enough solder for a really secure joint, reheat it and add more. If solder has created a connection that shouldnโt be there, use a utility knife to make two parallel cuts in the solder, and scrape away the little section between them.
Generally, I insert three or four components, trim the wires approximately, solder them, trim their wires finally, then pause to check the joints and the placement. If I solder too many components in succession, thereโs a greater risk of missing a bad joint, and if I make an error in placing a component, undoing it will be much more problematic if I have already added a whole lot more components around it.
Figures 3-80 and 3-81 show the version of this project that I constructed, before I trimmed the board to the minimum size.
Figure 3-80. Components mounted on a piece of perforated board.
Figure 3-81. The assembly seen from below. The copper circles around the holes are not necessary for this project. Some of them have picked up some solder, but this is irrelevant as long as no unintentional short circuits are created.
Flying Wire Segments
The jaws of your wire cutters exert a powerful force that peaks and then is suddenly released when they cut through wire. This force can be translated into sudden motion of the snipped wire segment. Some wires are relatively soft, and donโt pose a risk, but harder wires can fly in unpredictable directions at high speed, and may hit you in the eye. The leads of transistors are especially hazardous in this respect.
I think itโs a good idea to wear safety glasses when trimming wires.
Finishing the Job
I always use bright illumination. This is not a luxury; it is a necessity. Buy a cheap desk lamp if you donโt already have one. I use a daylight-spectrum fluorescent desk lamp, because it helps me identify the colored bands on resistors more reliably. Note that this type of fluorescent lamp emits quite a lot of ultraviolet light, which is not good for the lens in your eye. Avoid looking closely and directly at the tube in the lamp, and if you wear glasses, they will provide additional protection.
No matter how good your close-up vision is, you need to examine each joint with that close-up magnifier. Youโll be surprised how imperfect some of them are. Hold the magnifier as close as possible to your eye, then pick up the thing that you want to examine and bring it closer until it comes into focus.
Finally, you should end up with a working circuit. You can insert the wires from your power supply into two of the tiny power sockets, and plug a red LED into the remaining two sockets. Remember that the two center sockets are negative, and the two outer sockets are positive, because it was easier to wire the circuit this way. You should color-code them to avoid mistakes.
So now you have a tiny circuit that pulses like a heartbeat. Or does it? If you have difficulty making it work, retrace every connection and compare it with the schematic. If you donโt find an error, apply power to the circuit, attach the black lead from your meter to the negative side, and then go around the circuit with the red lead, checking the presence of voltage. Every part of this circuit should show at least some voltage while itโs working. If you find a dead connection, you may have made a bad solder joint, or missed one entirely.
When youโre done, now what? Well, now you can stop being an electronics hobbyist and become a crafts hobbyist. You can try to figure out a way to make this thing wearable.
First you have to consider the power supply. Because of the components that I used, we really need 9 volts to make this work well. How are you going to make this 9-volt circuit wearable, with a bulky 9-volt battery?
I can think of three answers:
1. You can put the battery in a pocket, and mount the flasher on the outside of the pocket, with a thin wire penetrating the fabric. Note that the tiny power connector on the perforated board will accept two 22-gauge wires if they are solid core, or if they are stranded (like the wires from a 9-volt battery connector) but have been thinly coated with solder.
2. You could mount the battery inside the crown of a baseball cap, with the flasher on the front.
3. You can put together three 3-volt button batteries in a stack, held in some kind of plastic clip. If you try this option, it may not be a good idea to try to solder wire to a battery. You will heat the liquid stuff inside the battery, which may not be good for it, and may not be good for you if the liquid starts boiling and the battery bursts open. Also, solder doesnโt stick easily to the metallic finish on most battery terminals.
Most LEDs create a sharply defined beam of light, which you may want to diffuse to make it look nicer. One way to do this is to use a piece of transparent acrylic plastic, at least 1/4 inch thick, as shown in Figure 3-82. Sandpaper the front of the acrylic, ideally
Comments (0)