Shop Management by Frederick Winslow Taylor (top books to read .TXT) đź“•
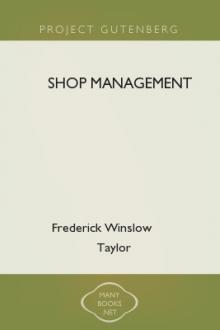
In referring to high wages and low labor cost as fundamental in good management, the writer is most desirous not to be misunderstood.
By high wages he means wages which are high only with relation to the average of the class to which the man belongs and which are paid only to those
Read free book «Shop Management by Frederick Winslow Taylor (top books to read .TXT) 📕» - read online or download for free at americanlibrarybooks.com
- Author: Frederick Winslow Taylor
- Performer: -
Read book online «Shop Management by Frederick Winslow Taylor (top books to read .TXT) 📕». Author - Frederick Winslow Taylor
endeavor continually to force the men toward this “standard time,” while
the workmen constantly use every effort to prevent this from being done
and to lead the management in the wrong direction. In spite of this
conflict, however, the “standard time” is gradually approached.
Under the Towne-Halsey plan the management gives up all direct effort to
reach this “quickest time,” but offers mild inducements to the workmen
to do so, and turns over the whole enterprise to them. The workmen,
peacefully as far as the management is concerned, but with considerable
pulling and hauling among themselves, and without the assistance of a
trained guiding hand, drift gradually and slowly in the direction of the
“standard time,” but rarely approach it closely.
With accurate time study as a basis, the “quickest time” for each job
is at all times in plain sight of both employers and workmen, and is
reached with accuracy, precision, and speed, both sides pulling hard in
the same direction under the uniform simple and just agreement that
whenever a first-class man works his best he will receive from 30 to 100
per cent more than the average of his trade.
Probably a majority of the attempts that are made to radically change
the organization of manufacturing companies result in a loss of money to
the company, failure to bring about the change sought for, and a return
to practically the original organization. The reason for this being that
there are but few employers who look upon management as an art, and that
they go at a difficult task without either having understood or
appreciated the time required for organization or its cost, the troubles
to be met with, or the obstacles to be overcome, and without having
studied the means to be employed in doing so.
Before starting to make any changes in the organization of a company the
following matters should be carefully considered: First, the importance
of choosing the general type of management best suited to the particular
case. Second, that in all cases money must be spent, and in many cases a
great deal of money, before the changes are completed which result in
lowering cost. Third, that it takes time to reach any result worth
aiming at. Fourth, the importance of making changes in their proper
order, and that unless the right steps are taken, and taken in their
proper sequence, there is great danger from deterioration in the quality
of the output and from serious troubles with the workmen, often
resulting in strikes.
As to the type of management to be ultimately aimed at, before any
changes whatever are made, it is necessary, or at least highly
desirable, that the most careful consideration should be given to the
type to be chosen; and once a scheme is decided upon it should be
carried forward step by step without wavering or retrograding. Workmen
will tolerate and even come to have great respect for one change after
another made in logical sequence and according to a consistent plan. It
is most demoralizing, however, to have to recall a step once taken,
whatever may be the cause, and it makes any further changes doubly
difficult.
The choice must be made between some of the types of management in
common use, which the writer feels are properly designated by the word
“drifting,” and the more modern scientific management based on an
accurate knowledge of how long it should take to do the work. If, as is
frequently the case, the managers of an enterprise find themselves so
overwhelmed with other departments of the business that they can give
but little thought to the management of the shop, then some one of the
various “drifting” schemes should be adopted; and of these the writer
believes the Towne-Halsey plan to be the best, since it drifts safely
and peacefully though slowly in the right direction; yet under it the
best results can never be reached. The fact, however, that managers are
in this way overwhelmed by their work is the best proof that there is
something radically wrong with the plan of their organization and in
self defense they should take immediate steps toward a more thorough
study of the art.
It is not at all generally realized that whatever system may be used,
—providing a business is complex in its nature—the building up of an
efficient organization is necessarily slow and sometimes very expensive.
Almost all of the directors of manufacturing companies appreciate the
economy of a thoroughly modern, up-to-date, and efficient plant, and are
willing to pay for it. Very few of them, however, realize that the best
organization, whatever its cost may be, is in many cases even more
important than the plant; nor do they clearly realize that no kind of an
efficient organization can be built up without spending money. The
spending of money for good machinery appeals to them because they can
see machines after they are bought; but putting money into anything so
invisible, intangible, and to the average man so indefinite, as an
organization seems almost like throwing it away.
There is no question that when the work to be done is at all
complicated, a good organization with a poor plant will give better
results than the best plant with a poor organization. One of the most
successful manufacturers in this country was asked recently by a number
of financiers whether he thought that the difference between one style
of organization and another amounted to much providing the company had
an up-to-date plant properly located. His answer was, “If I had to
choose now between abandoning my present organization and burning down
all of my plants which have cost me millions, I should choose the
latter. My plants could be rebuilt in a short while with borrowed money,
but I could hardly replace my organization in a generation.”
Modern engineering can almost be called an exact science; each year
removes it further from guess work and from rule-of-thumb methods and
establishes it more firmly upon the foundation of fixed principles.
The writer feels that management is also destined to become more of an
art, and that many of the, elements which are now believed to be outside
the field of exact knowledge will soon be standardized tabulated,
accepted, and used, as are now many of the elements of engineering.
Management will be studied as an art and will rest upon well recognized,
clearly defined, and fixed principles instead of depending upon more or
less hazy ideas received from a limited observation of the few
organizations with which the individual may have come in contact. There
will, of course, be various successful types, and the application of the
underlying principles must be modified to suit each particular case. The
writer has already indicated that he thinks the first object in
management is to unite high wages with a low labor cost. He believes
that this object can be most easily attained by the application of the
following principles:
(a) A LARGE DAILY TASK. —Each man in the establishment, high or low,
should daily have a clearly defined task laid out before him. This task
should not in the least degree be vague nor indefinite, but should be
circumscribed carefully and completely, and should not be easy to
accomplish.
(b) STANDARD CONDITIONS. —Each man’s task should call for a full day’s
work, and at the same time the workman should be given such standardized
conditions and appliances as will enable him to accomplish his task with
certainty.
(c) HIGH PAY FOR SUCCESS. —He should be sure of large pay when he
accomplishes his task.
(d) LOSS IN CASE OF FAILURE. —When he fails he should be sure that
sooner or later he will be the loser by it.
When an establishment has reached an advanced state of organization, in
many cases a fifth element should be added, namely: the task should be
made so difficult that it can only be accomplished by a first-class man.
There is nothing new nor startling about any of these principles and yet
it will be difficult to find a shop in which they are not daily violated
over and over again. They call, however, for a greater departure from
the ordinary types of organization than would at first appear. In the
case, for instance, of a machine shop doing miscellaneous work, in order
to assign daily to each man a carefully measured task, a special
planning department is required to lay out all of the work at least one
day ahead. All orders must be given to the men in detail in writing; and
in order to lay out the next day’s work and plan the entire progress of
work through the shop, daily returns must be made by the men to the
planning department in writing, showing just what has been done. Before
each casting or forging arrives in the shop the exact route which it is
to take from machine to machine should be laid out. An instruction card
for each operation must be written out stating in detail just how each
operation on every piece of work is to be done and the time required to
do it, the drawing number, any special tools, jigs, or appliances
required, etc. Before the four principles above referred to can be
successfully applied it is also necessary in most shops to make
important physical changes. All of the small details in the shop, which
are usually regarded as of little importance and are left to be
regulated according to the individual taste of the workman, or, at best,
of the foreman, must be thoroughly and carefully standardized; such.
details, for instance, as the care and tightening of the belts; the
exact shape and quality of each cutting tool; the establishment of a
complete tool room from which properly ground tools, as well as jigs,
templates, drawings, etc., are issued under a good check system, etc.;
and as a matter of importance (in fact, as the foundation of scientific
management) an accurate study of unit times must be made by one or more
men connected with the planning department, and each machine tool must
be standardized and a table or slide rule constructed for it showing how
to run it to the best advantage.
At first view the running of a planning department, together with the
other innovations, would appear to involve a large amount of additional
work and expense, and the most natural question would be is whether the
increased efficiency of the shop more than offsets this outlay? It must
be borne in mind, however, that, with the exception of the study of unit
times, there is hardly a single item of work done in the planning
department which is not already being done in the shop. Establishing a
planning department merely concentrates the planning and much other
brainwork in a few men especially fitted for their task and trained in
their especial lines, instead of having it done, as heretofore, in most
cases by high priced mechanics, well fitted to work at their trades, but
poorly trained for work more or less clerical in its nature.
There is a close analogy between the methods of modern engineering and
this type of management. Engineering now centers in the drafting room as
modern management does in the planning department. The new style
engineering has all the appearance of complication and extravagance,
with its multitude of drawings; the amount of study and work which is
put into each detail; and its corps of draftsmen, all of whom would be
sneered at by the old engineer as “non-producers.” For the same reason,
modern management, with its minute time study and a managing department
in which each operation is carefully planned, with its many
Comments (0)