Shop Management by Frederick Winslow Taylor (top books to read .TXT) π
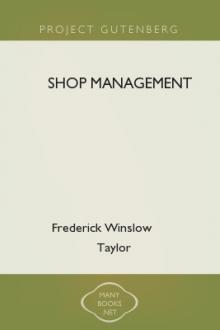
In referring to high wages and low labor cost as fundamental in good management, the writer is most desirous not to be misunderstood.
By high wages he means wages which are high only with relation to the average of the class to which the man belongs and which are paid only to those
Read free book Β«Shop Management by Frederick Winslow Taylor (top books to read .TXT) πΒ» - read online or download for free at americanlibrarybooks.com
- Author: Frederick Winslow Taylor
- Performer: -
Read book online Β«Shop Management by Frederick Winslow Taylor (top books to read .TXT) πΒ». Author - Frederick Winslow Taylor
considerable part of their time in partial idleness, talking and half
working, or in actually doing nothing.
Talking while at work was stopped by seating them far apart. The hours
of work were shortened from 10 1/2 per day, first to 9 1/2, and later to
8 1/2; a Saturday half holiday being given them even with the shorter
hours. Two recesses of ten minutes each were given them, in the middle
of the morning and afternoon, during which they were expected to leave
their seats, and were allowed to talk.
The shorter hours and improved conditions made it possible for the girls
to really work steadily, instead of pretending to do so. Piece work was
then introduced, a differential rate being paid, not for an increase in
output, but for greater accuracy in the inspection; the lots inspected
by the over-inspectors forming the basis for the payment of the
differential. The work of each girl was measured every hour, and they
were all informed whether they were keeping up with their tasks, or how
far they had fallen short and an assistant was sent by the foreman to
encourage those who were falling behind, and help them to catch up.
The principle of measuring the performance of each workman against a
standard at frequent intervals, of keeping them informed as to their
progress, and of sending an assistant to help those who were falling
down, was carried out throughout the works, and proved to be most
useful.
The final results of the improved system in the inspecting department
were as follows:
(a) Thirty-five girls did the work formerly done by one hundred and
twenty.
(b) The girls averaged from $6.50 to $9.00 per week instead of $3.50 to
$4.50, as formerly.
(c) They worked only 8 1/2 hours per day, with Saturday a half-holiday,
while they had formerly worked 10 1/2 hours per day.
(d) An accurate comparison of the balls which were inspected under the
old system of day work with those done under piece work, with
over-inspection, showed that, in spite of the large increase in output
per girl, there were 58 per cent more defective balls left in the
product as sold under day work than under piece work. In other words,
the accuracy of inspection under piece work was one-third greater than
that under day work.
That thirty-five girls were able to do the work which formerly required
about one hundred and twenty is due, not only to the improvement in the
work of each girl, owing to better methods, but to the weeding out of
the lazy and unpromising candidates, and the substitution of more
ambitious individuals.
A more interesting illustration of the effect of the improved conditions
and treatment is shown in the following comparison. Records were kept of
the work of ten girls, all βold hands,β and good inspectors, and the
improvement made by these skilled hands is undoubtedly entirely due to
better management. All of these girls throughout the period of
comparison were engaged on the same kind of work, viz.: inspecting
bicycle balls, three-sixteenths of an inch in diameter.
The work of organization began in March, and although the records for
the first three months were not entirely clear, the increased output due
to better day work amounted undoubtedly to about 33 per cent. The
increase per day from June on day work, to July on piece work, the hours
each month being 10 1/2 per day, was 37 per cent. This increase was due
to the introduction of piece work. The increase per day from July to
August (the length of working days in July being 10 1/2 hours, and in
August 9 1/2 hours, both months piece work) was 33 per cent.
The increase from August to September (the length of working day in
August being 9 1/2 hours, and in September 8 1/2 hours) was 0.08 per
cent This means that the girls did practically the same amount of work
per day in September, in 8 1/2 hours, that they did in August in 9 1/2
hours.
To summarize: the same ten girls did on an average each day in
September, on piece work, when only working 8 1/2 hours per day, 2.42
times as much, or nearly two and one-half times as much, in a day (not
per hour, the increase per hour was of course much greater) as they had
done when working on day work in March with a working day of 10 1/2
hours. They earned $6.50 to $9.00 per week on piece work, while they had
only earned $3.50 to $4.50 on day work. The accuracy of inspection under
piece work was one-third greater than under day work.
The time study for this work was done by my friend, Sanford E. Thompson,
C. E. who also had the actual management of the girls throughout the
period of transition. At this time Mr. H. L. Gantt was general
superintendent of the company, and the work of systematizing was under
the general direction of the writer. It is, of course, evident that the
nature of the organizations required to manage different types of
business must vary to an enormous extent, from the simple tonnage works
(with its uniform product, which is best managed by a single strong man
who carries all of the details in his head and who, with a few
comparatively cheap assistants, pushes the enterprise through to
success) to the large machine works, doing a miscellaneous business,
with its intricate organization, in which the work of any one man
necessarily counts for but little.
It is this great difference in the type of the organization required
that so frequently renders managers who have been eminently successful
in one line utter failures when they undertake the direction of works of
a different kind. This is particularly true of men successful in tonnage
work who are placed in charge of shops involving much greater detail.
In selecting an organization for illustration, it would seem best to
choose one of the most elaborate. The manner in which this can be
simplified to suit a less intricate case will readily suggest itself to
any one interested in the subject. One of the most difficult works to
organize is that of a large engineering establishment building
miscellaneous machinery, and the writer has therefore chosen this for
description.
Practically all of the shops of this class are organized upon what may
be called the military plan. The orders from the general are transmitted
through the colonels, majors, captains, lieutenants and noncommissioned
officers to the men. In the same way the orders in industrial
establishments go from the manager through superintendents, foremen of
shops, assistant foremen and gang bosses to the men. In an establishment
of this kind the duties of the foremen, gang bosses, etc., are so
varied, and call for an amount of special information coupled with such
a variety of natural ability, that only men of unusual qualities to
start with, and who have had years of special training, can perform them
in a satisfactory manner. It is because of the difficultyβalmost the
impossibility of getting suitable foremen and gang bosses, more than for
any other reason, that we so seldom hear of a miscellaneous machine
works starting in on a large scale and meeting with much, if any,
success for the first few years. This difficulty is not fully realized
by the managers of the old well established companies, since their
superintendents and assistants have grown up with the business, and have
been gradually worked into and fitted for their especial duties through
years of training and the process of natural selection. Even in these
establishments, however, this difficulty has impressed itself upon the
managers so forcibly that most of them have of late years spent
thousands of dollars in re-grouping their machine tools for the purpose
of making their foremanship more effective. The planers have been placed
in one group, slotters in another, lathes in another, etc., so as to
demand a smaller range of experience and less diversity of knowledge
from their respective foremen.
For an establishment, then, of this kind, starting up on a large scale,
it may be said to be an impossibility to get suitable superintendents
and foremen.
The writer found this difficulty at first to be an almost insurmountable
obstacle to his work in organizing manufacturing establishments; and
after years of experience, overcoming the opposition of the heads of
departments and the foremen and gang bosses, and training them to their
new duties, still remains the greatest problem in organization. The
writer has had comparatively little trouble in inducing workmen to
change their ways and to increase their speed, providing the proper
object lessons are presented to them, and time enough is allowed for
these to produce their effect. It is rarely the case, however, that
superintendents and foremen can find any reasons for changing their
methods, which, as far as they can see, have been successful. And
having, as a rule, obtained their positions owing to their unusual force
of character, and being accustomed daily to rule other men, their
opposition is generally effective.
In the writerβs experience, almost all shops are under-officered.
Invariably the number of leading men employed is not sufficient to do
the work economically. Under the military type of organization, the
foreman is held responsible for the successful running of the entire
shop, and when we measure his duties by the standard of the four leading
principles of management above referred to, it becomes apparent that in
his case these conditions are as far as possible from being fulfilled.
His duties may be briefly enumerated in the following way. He must lay
out the work for the whole shop, see that each piece of work goes in the
proper order to the right machine, and that the man at the machine knows
just what is to be done and how he is to do it. He must see that the
work is not slighted, and that it is done fast, and all the while he
must look ahead a month or so, either to provide more men to do the work
or more work for the men to do. He must constantly discipline the men
and readjust their wages, and in addition to this must fix piece work
prices and supervise the timekeeping.
The first of the four leading principles in management calls for a
clearly defined and circumscribed task. Evidently the foremanβs duties
are in no way clearly circumscribed. It is left each day entirely to his
judgment what small part of the mass of duties before him it is most
important for him to attend to, and he staggers along under this
fraction of the work for which he is responsible, leaving the balance to
be done in many cases as the gang bosses and workmen see fit. The second
principle calls for such conditions that the daily task can always be
accomplished. The conditions in his case are always such that it is
impossible for him to do it all, and he never even makes pretence of
fulfilling his entire task. The third and fourth principles call for
high pay in case the task is successfully done, and low pay in case of
failure. The failure to realize the first two conditions, however,
renders the application of the last two out of the question.
The foreman usually endeavors to lighten his burdens by delegating his
duties to the various assistant foremen or gang bosses in charge of
lathes, planers, milling machines, vise work, etc. Each of these men is
then called upon to perform duties of almost as great variety as those
of the foreman himself. The difficulty in obtaining in one man the
variety of special information and the different mental and
Comments (0)